포스코 포항제철소(소장 이백희)의 2고로가 빅데이터와 AI를 활용해 쇳물을 생산하며, 미래 제철소의 새로운 모습으로 떠오르고 있다.
포항제철소 2고로는 2017년 이후 5년에 걸쳐 스마트팩토리 기술을 적용한 '스마트 고로' 형태로 운용되며, 기존 조업 기술을 성공적으로 대체하고 있다.
철광석을 녹여 쇳물을 만드는 고로의 내부 온도는 최대 2300도까지 치솟기 때문에 고로 내부를 육안으로 확인하는 것이 불가능하다. 기존에는 표면의 온도, 압력, 가스 성분으로 용광로 내부의 상황을 추정했고, 고로 운전 또한 수동제어로 실시됐기 때문에 제철 공정은 숙련된 직원의 경험에 의존하는 프로세스로 여겨져 왔다.
하지만 새롭게 제시된 '스마트 고로'는 실시간 측정된 데이터로 수많은 케이스를 학습하고, 용광로 상태를 스스로 체크해 조업 결과를 미리 예측할 수 있다. 이에 포스코는 스마트팩토리 기술개발을 위해 2018년 산·학·연의 '스마트 고로' 협력체계를 구성했다.
세계 최고 수준의 조업 기술을 보유한 포스코와 더불어 IoT 센서 및 영상처리기술과 빅데이터 솔루션을 제공하는 국내 벤처기업, AI 알고리즘을 개발하는 지역 대학·연구소가 세계 최초의 인공지능 활용 고로 자동제어를 위해 머리를 맞댄 것이다.
산·학·연 협업 체계 구축을 시작으로, 포스코 고유의 스마트팩토리 인프라인 '포스프레임(PosFrame)'이 적용됐고, 시범운영을 거쳐 2019년부터는 본격적으로 전 제철소 스마트화에 나섰으며, 2020년에는 조업을 넘어 설비·물류·안전·사무 등으로 스마트팩토리 적용 범위를 확대하게 됐다.
포항제철소 2고로의 스마트 고로 도입은 철강 생산량 증대와 품질 향상에 획기적으로 기여하고 있으며, 연 8만 5천 톤의 생산량이 증가했고, 품질 불량률 또한 기존 대비 63% 감소했다. 8만 5천 톤의 철강 생산량은 중형 승용차를 연간 8만 5천대 더 생산할 수 있는 양이다.
이뿐만이 아니다. 수동제어가 자동제어로 전환되니 작업자의 안전도가 향상됐고, 단순, 반복 업무에서 벗어나 직원의 창의성을 발휘해 성과를 낼 수 있는 기회도 얻게 됐다.
포항제철소 2고로는 이러한 성과에 힘입어 2019년 대한민국 최초로 세계경제포럼(WEF)에 의해 '등대공장'에 선정되기도 했으며, 2고로에 적용한 스마트팩토리 기술을 3, 4고로로 확대 적용해 운영하고 있다.
한편, 포스코는 포항제철소 2고로에서 얻은 스마트 공장 구축 노하우를 국내 기업에 전수하고 있으며, 포스코와 중소벤처기업부가 각각 200억, 100억 원을 출연해 스마트팩토리 기술 지원사업을 실시하고 있다. 포스코는 2023년까지 1000개 기업에 기술 지원을 목표로 하고 있다.
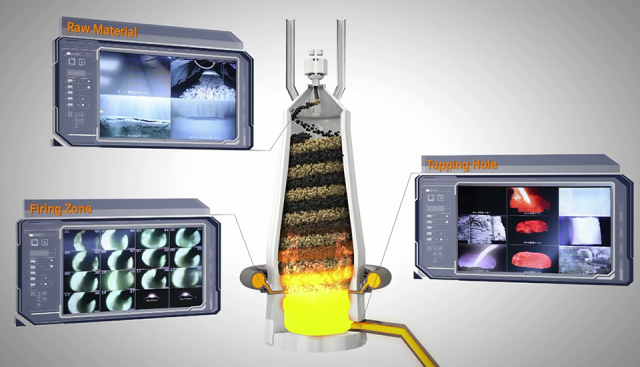
전체댓글 0